Semco SI SSWM 3X 5000A/6000A/8000A – Single Side Automatic Spot Welding Machine – Pneumatic/Fully Electric
Table Of Content
- Overview
- Main Features
- Main Technical Parameters
- Main Configuration
- Technical Support Services
Introduction to the Equipment:
SI SSWM 3X 5000A automatic spot welding machine is a multi-axis motion controller developed by modern automation expert technology, with precision transmission and motor control mechanism, automatic walking mechanism, precision welding power supply, and effective real-time control processing automatic production equipment. Combined with the company’s many years of experience in spot welding in the lithium battery industry,
we develop and design for the application scenarios in the automatic welding production of lithium battery packs. The welding efficiency is high, the welding quality is good, the positioning is accurate, it is suitable for many products, the performance is stable, and the maintenance is simple and convenient. It is the first choice for automatic welding production such as lithium battery PACK welding.
Equipment Action Flow:
Load cells/supports/batteries into the fixture→→Place the fixture to the induction position →→Automatic spot welding of the equipment→→Manually flip and automatically weld the other side →→Remove the battery pack from the fixture→→Continue uninterrupted at the left and right positions Spot welding production.
3. The overall dimensions and appearance of the equipment (width*length*height): 1000*800*1680 (this size is for reference only).
Main Features:
1. Double-station non-stop continuous automatic spot welding operation.
2. Automatic welding current monitoring and alarm function.
3. Forced escape loop water cooling function.
4. Rotating welding head can spot weld nickel plates with different angles. (Optional function)
5. The anti-sticking needle function can be turned on and off by rotating the welding needle. (Optional function)
6. All imported servo motor configuration.
7. Electric drive pressure welding head to make the pressure more precise.
8. Automatic alarm for defective solder joints, manual control and automatic positioning repair welding.
9. A variety of programming methods, easy to learn.
10. Three-level operating authority setting, convenient file management.
11. The energy of different solder joints can be switched during the welding process.
12. Output setting, production counting, quantitative shutdown.
13. Set the number of times the solder pins are used, and remind the solder pins to maintain after reaching the stipulation.
Equipment Technical Parameters:
1 Power supply specifications: Power supply: single-phase 220V 50/60HZ 2.8KW.
2 Air source specifications: Air supply connector PP20, trachea PU D=8MM L=2M, pressure 0.3MP- 0.8MP, flow rate 0.02M2/h.
3 Equipment weight: 126KG
4 Maximum stroke: X 600MM, Y 400MM.
5 Workpiece height: 50MM—200MM
6 Welding pin pressing stroke: 10—30MM
7 Welding head pressure: 1-5KGF, optional and adjustable
8 Configuration welding pin chuck: 1.7MM imported spot welding pin and chuck (optional)
9 Welding head rotation angle: 90O ((Need to be customized)
10 Welding platform load: 35KG (maximum)
11 Welding speed: 3000 points/hour
12 Number of operators: 1
13 Equipment environmental requirements:
13.1 Ambient temperature: 0°C-40°C.
13.2 Relative humidity: 30%~85%.
13.3 Atmospheric pressure: 750±30mmHg.
13.4 There is no strong electromagnetic field interference and corrosive gas erosion.
13.5 Measure 1000mm away from the outer wall of the machine.
13.6 The equipment complies with the national safety standards of relevant equipment.
Main Configuration:
S. No. | Configuration | Quantity | Brand |
1 | Transistor welding power supply | 1 set | Red Lopard |
2 | Motion Controller | 1 set | Control |
3 | Touch screen | 1 piece | Weilun |
4 | servo motor | 3 sets | Matsushita |
5 | Stepper motor | 1 piece | Lei Sai/Penghui |
6 | The electromagnetic valve | 2 pcs | AirTAC |
7 | Bearing seat | 2 sets | TBI |
8 | Linear Guides | 3 sets | Shanghai Bank |
9 | 24V switching power supply | 1 piece | Zhenghua |
10 | sensor | 5 pcs | Omron/Taibang |
11 | Button + indicator | 5 pcs | Taiwan |
12 | Relay | 3 pcs | Izumi/Chint |
13 | Water circulation cooling system | 1 set | Red Leopard |
Equipment Configuration and Accessories List:
S.No. | Name | Brand | Model | Quantity | Unit | Remark |
1 | Single-sided automatic welding host platform | Semco | SI SSWM 3X 5000A | 1 | tower | |
2 | Welding power | Semco | Transistor MTB- 5000A | 1 | tower | |
3 | Active escape ring forced water Cold machine | DN | CW-3000 | 1 | tower | (Optional Pieces) |
4 | Allen wrench | Metric | 1 | set | ||
5 | Solder pin | Taiwan | D=1.7MMX100MM | 4 | Only | 2 only installed |
6 | Air hose | Semco | D=8MM L=2M +PP20 | 1 | Piece | |
7 | manual | Semco | SI SSWM 3X 5000A | 1 | Book | |
8 | Certificate of conformity | Semco | SI SSWM 3X 5000A | 1 | Piece |
List of Daily Consumption Materials:
S.No. | Name | Specification | Remark |
1 | Solder pin | D=1.7MM |
Equipment Installation and Training Content:
9.1 Equipment operation
9.1.1 After quickly setting the origin of the workpiece coordinate, it will automatically correspond to each welding this origin.
9.1.2 Adjusting the welding head stroke mechanism
9.1.3 Clamping solder pins
9.1.4 Set welding machine parameters
9.2 Daily maintenance.
9.3 Elimination and maintenance of common faults.
9.4 Use of software:
9.4.1 Personalized writing spot welding program (easy to learn one hour to learn)
9.4.2 Processing programming on the computer
Information Provision:
Equipment information: equipment operation manual and electronic version.
Equipment Acceptance:
- Delivery acceptance is carried out by the buyer. After the contract equipment arrives at the buyer, the buyer will unpack and accept the contract equipment, inspect the appearance of the contract equipment, and count the quantity of the contract equipment.
- The contract equipment is qualified for delivery and acceptance after unpacking, and the buyer will conduct an unpacking acceptance visa for the contract equipment.
- The unpacking acceptance is unqualified due to the seller’s design, manufacturing, and transportation quality defects, which delays the visa application. The seller shall bear the responsibility for the installation and commissioning of the equipment in the wrong contract.
Technical Support Services:
13.1 Training: The seller is responsible for technical training on the operation and maintenance of the buyer’s personnel. After the training, the trainees can independently operate, judge and deal with general failures.
13.2 Cooperate with the buyer to complete the on-site installation and commissioning of the equipment.
13.3 Possess technical support capabilities, after-sales service facilities and spare parts warehouse.
13.4 After receiving the user’s emergency notification of failure, respond within 8 hours. If you need to send someone to the site for maintenance, you should arrive at the user site within hours.
13.5 After the end of the warranty period, the seller will provide lifetime technical suppor
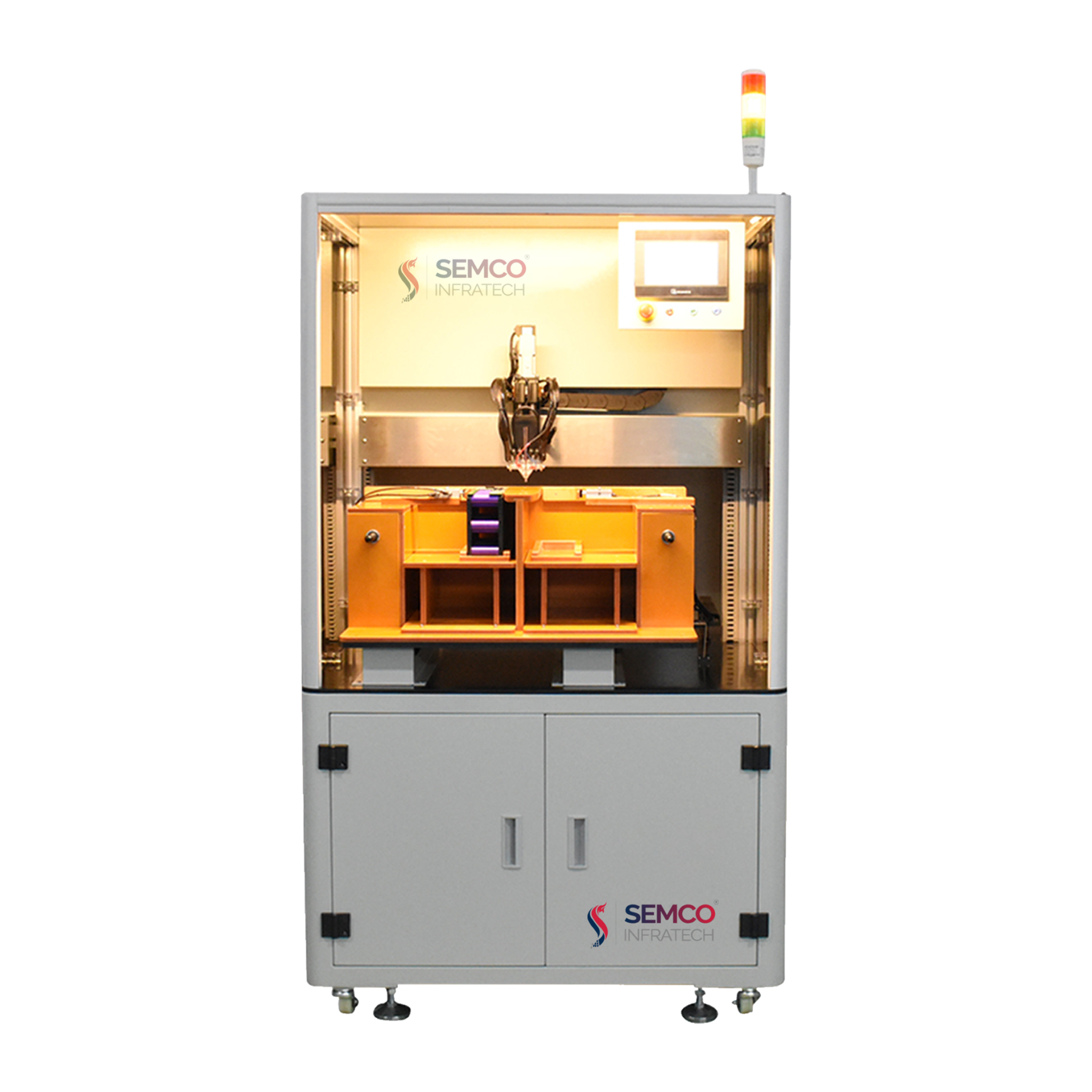
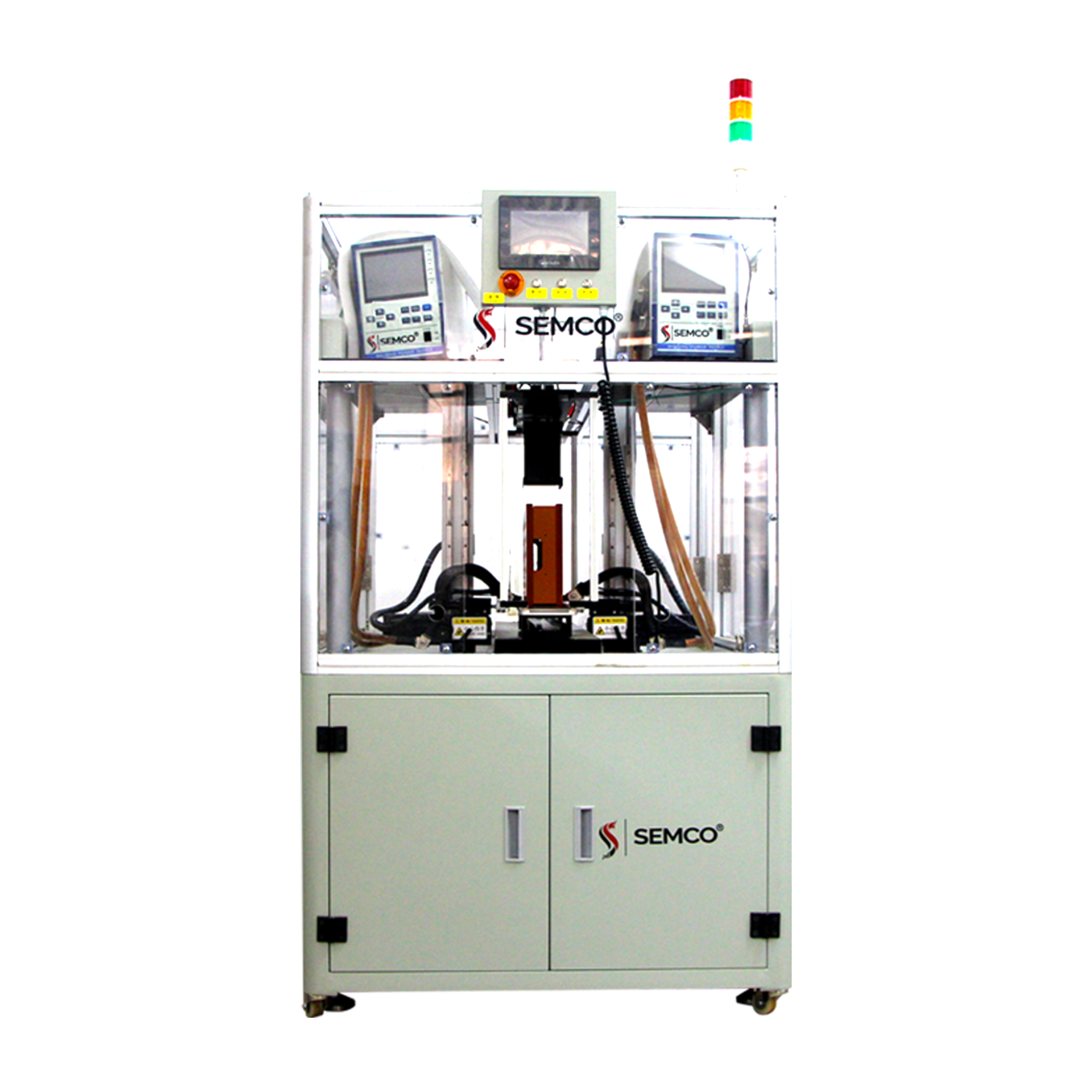